In May 2021, University of Arizona’s Tech Park became the new home for the test cell, mirror simulator, and actuator calibration system. Now, they will undergo testing to validate the mirror’s active support control system functionality and to guarantee that it is safe for mirror installation.
Get to know more: watch the first episode of Allure of the Universe, available at the GMT Brasil Youtube channel.
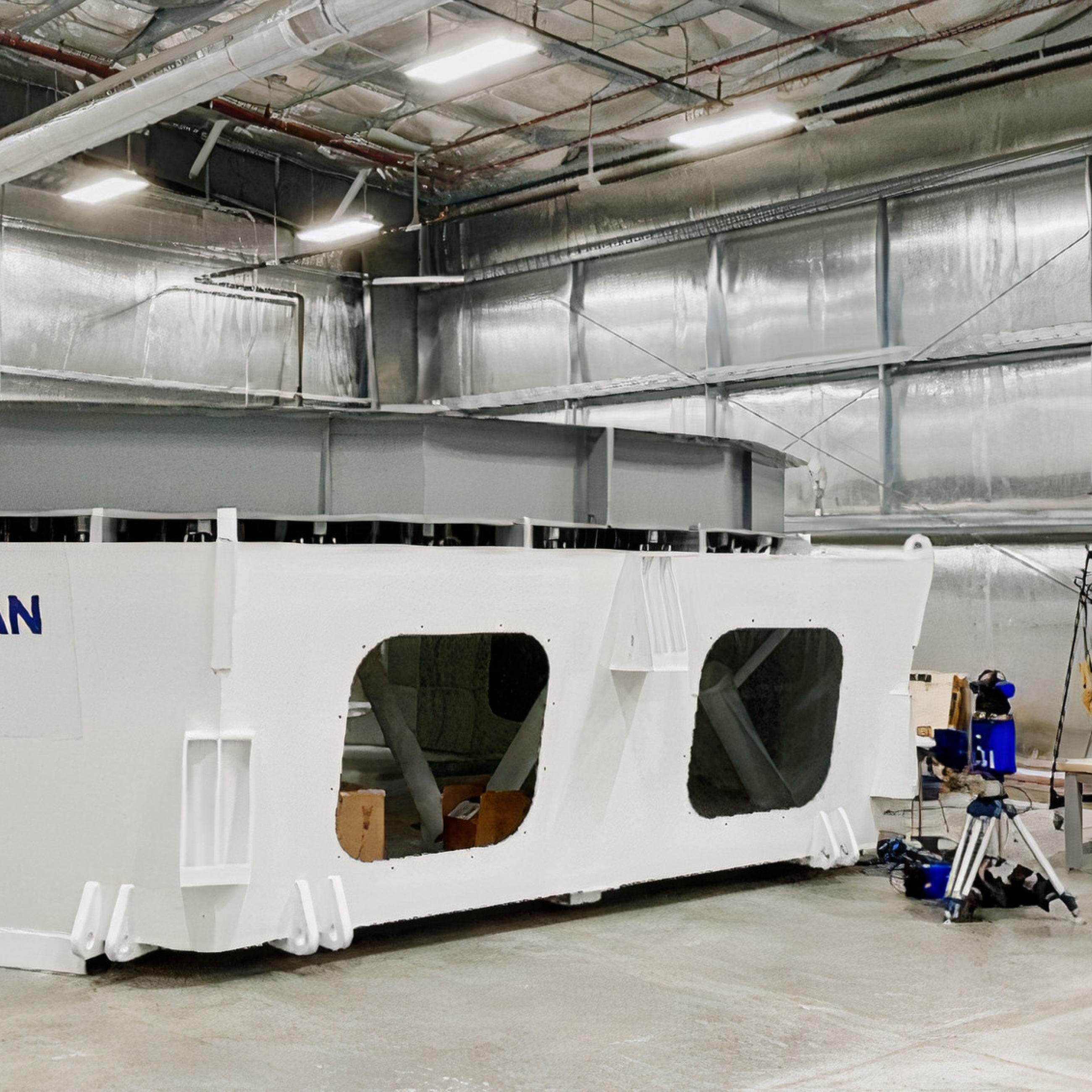
NEW TESTS FOR THE GMT TELESCOPE
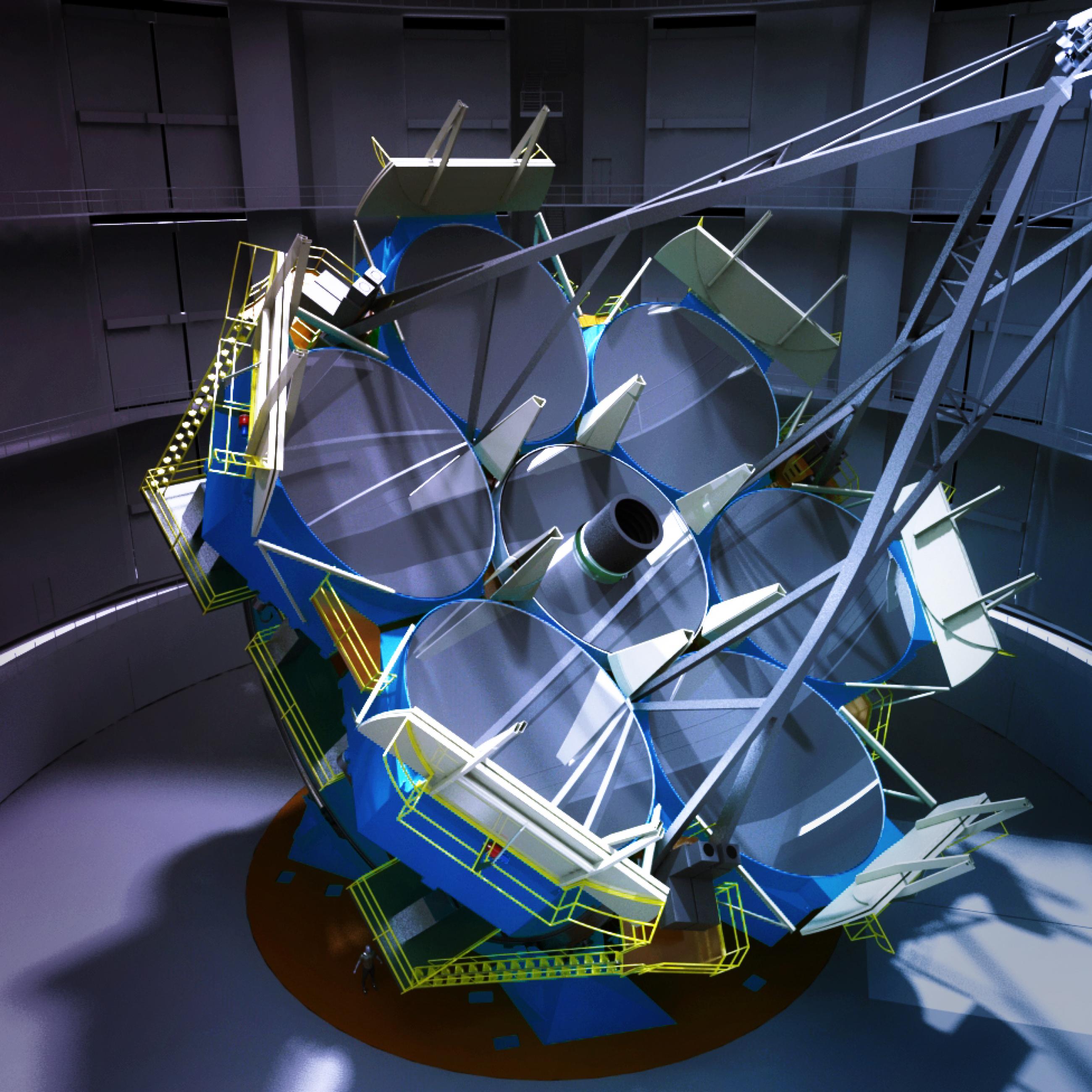
HOW TO MOVE THE TELESCOPE WITHOUT FRICTION?
The GMT telescope will weigh approximately 2,106 tons. It will float on a 50 microns thick film of oil, which is half as thick as a paper sheet. A micron equals one-thousandth of a millimeter or one-millionth of a meter, which will allow the GMT to essentially move without friction, due to its ability to compensate for Earth’s rotation, while tracking celestial bodies throughout the night sky.
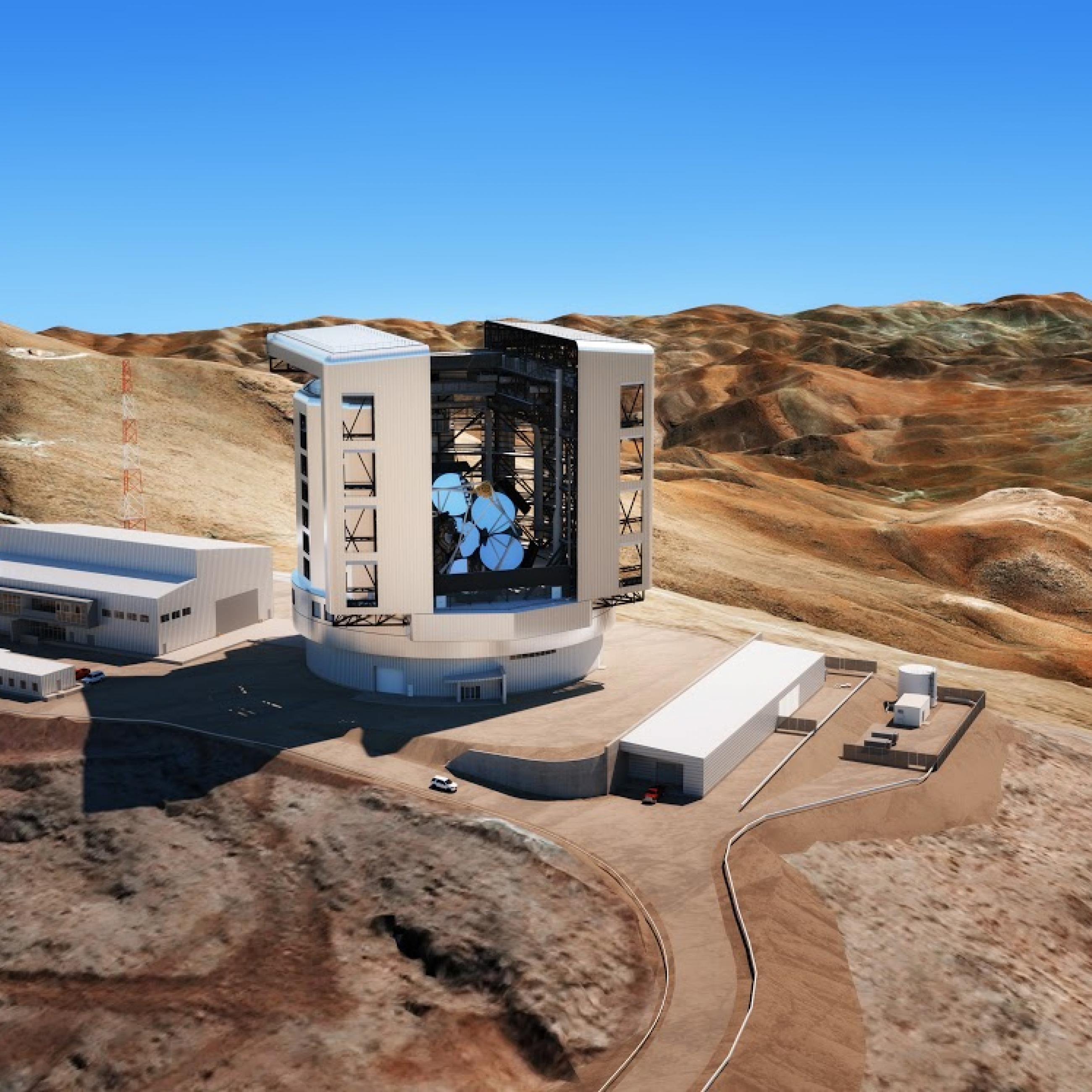
GET TO KNOW THE CONSTRUCTION SITE
Cerro Las Campanas, at the Las Campanas Observatory (LCO), Atacama Desert, will be home to one of the world’s biggest ground-based telescopes. The mountain is 2,500 meters high and known for its outstanding seeing with over 300 nights of clear skies per year - a result of being in a desert region, where there is only a small occurrence of clouds.
The preparations of the GMT mountaintop site began in 2012, but it only entered the construction phase after being authorized in 2015. Over 250 people work at the construction site. When the GMT is up and running, it is expected to employ 100-150 chileans professionals in technical, administrative and support positions.
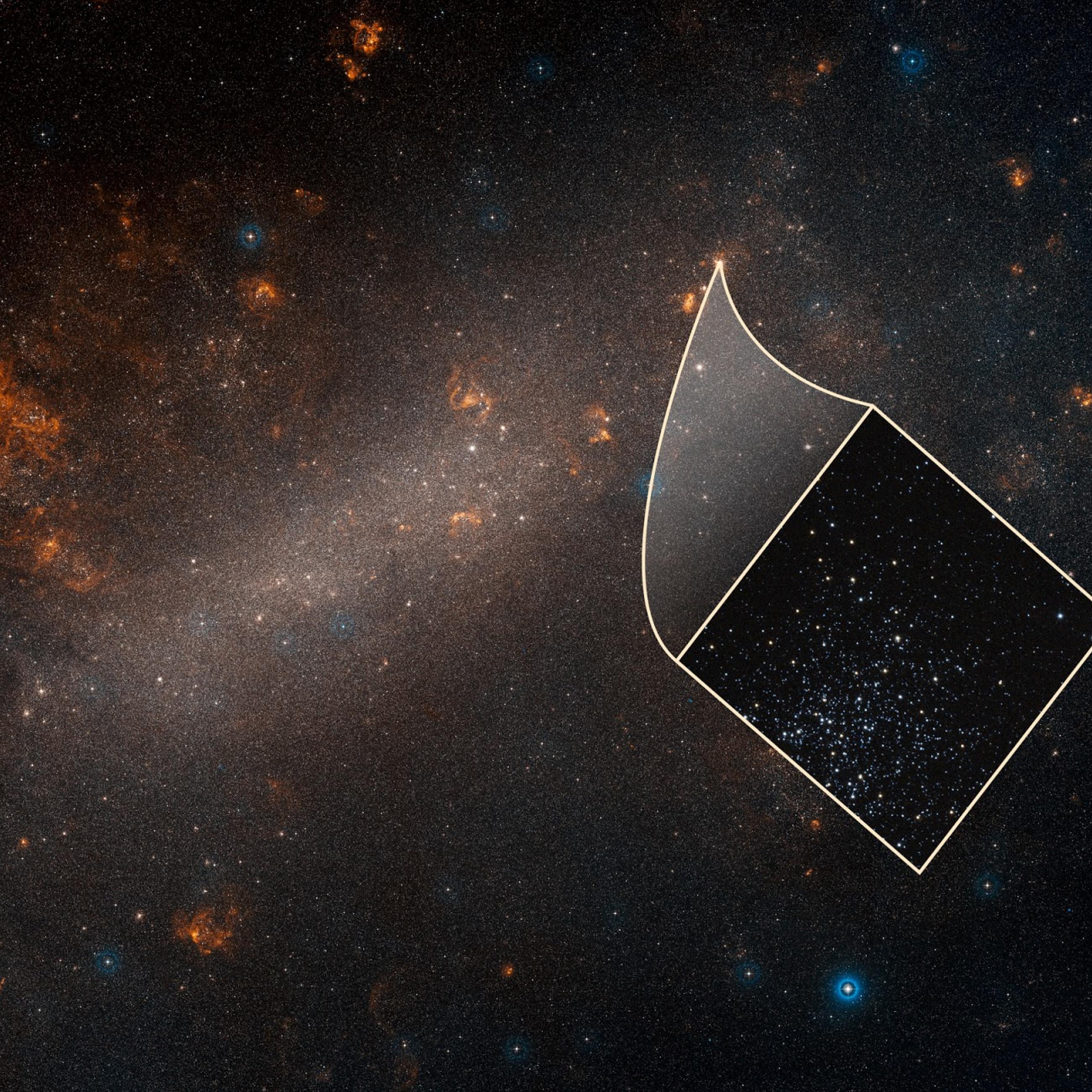
THE INSPIRATION BEHIND NAMING THE GMT
The Large Magellanic Cloud, namesake to the telescope, is a dwarf satellite galaxy located in the Milky Way. The name was given by the portuguese navigator Fernão de Magalhães (1480-1521) during one of these voyages at the beginning of the 16th century. - he also observed the Small Magellanic Cloud, which is a neighboring dwarf galaxy.
They cannot be seen from the Northern Hemisphere, being studied by southern telescopes, and are visible to the naked eye on nights of clear skies in January.
Unlike other satellite galaxies, they continue to form new stars at an accelerated rate,which helps scientists understand how galaxies are formed and evolve throughout time.
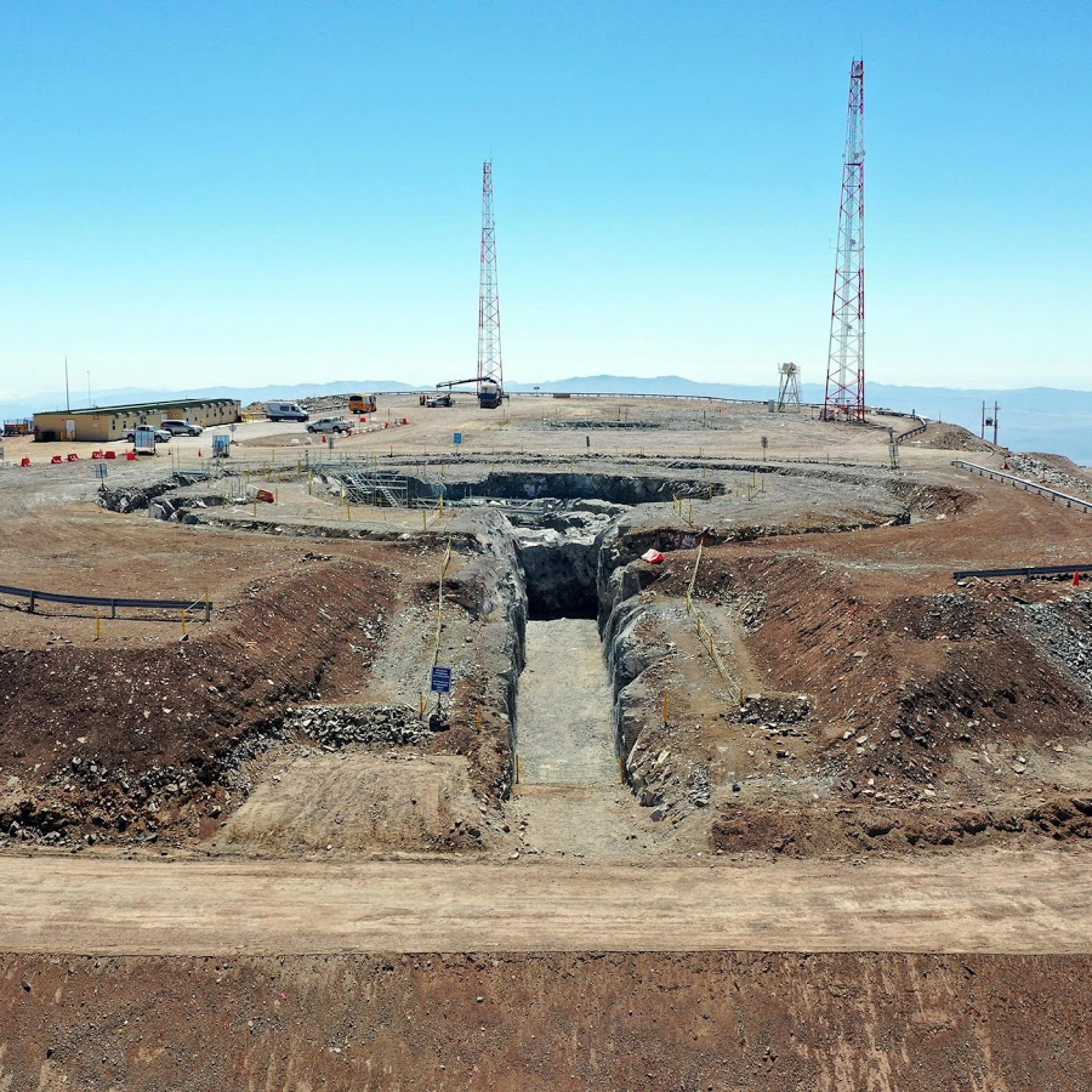
SEISMIC PROTECTION SYSTEM
To protect the 22-store building and avoid damage to its instruments, the project had to design an innovative protection system that successfully met the requirements of an independent review panel of internationally renowned experts.
The first line of defense is a seismic isolation system made of 24 single friction pendulum isolators that protect the telescope’s optical components and instruments from active ground motion caused by a major earthquake. These devices slide over a concave surface and it results in a pendulum-like motion. In addition, there is a hydraulic system that can return the 6,200 metric ton telescope structure to its operational position following an earthquake.
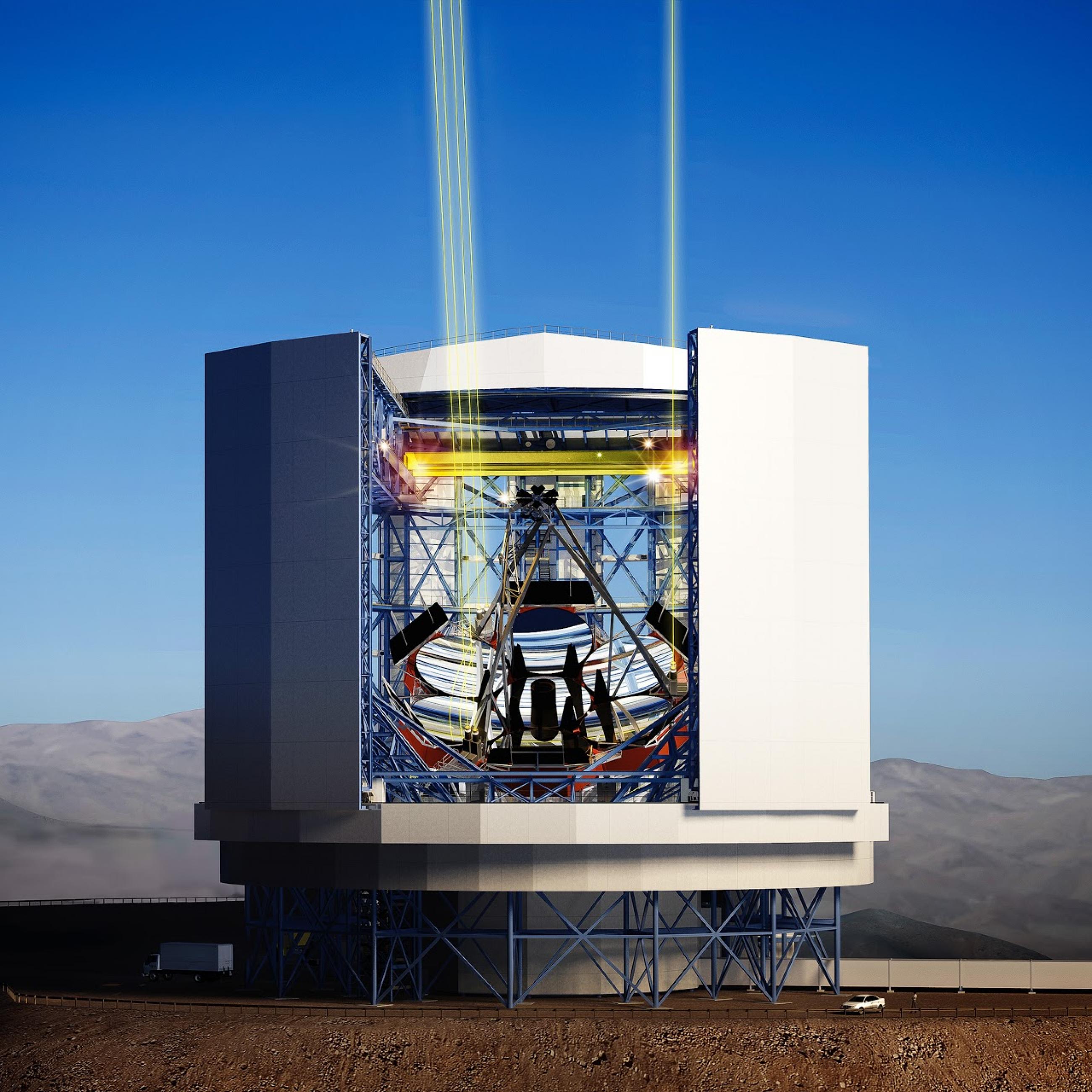
THE SECONDARY MIRRORS
The GMT will have 7 separate, circular segments each are 1.05 meters in diameter with the same geometry as the primary segments, which are capable of correcting images blurred by the atmospheric distortion effect.
This system will allow capturing clear pictures to help studying even smaller and more distant objects with minimized distortions. Each secondary mirror has 675 actuators controlled by computers that will continuously adjust and deform the mirrors according to the patterns caused by atmospheric turbulences.
Its adaptive optics technology will guarantee that the adjustments made to correct such distortions apply to all instruments, unlike other systems in which this correction takes place within specific instruments and, therefore, applies only to them.
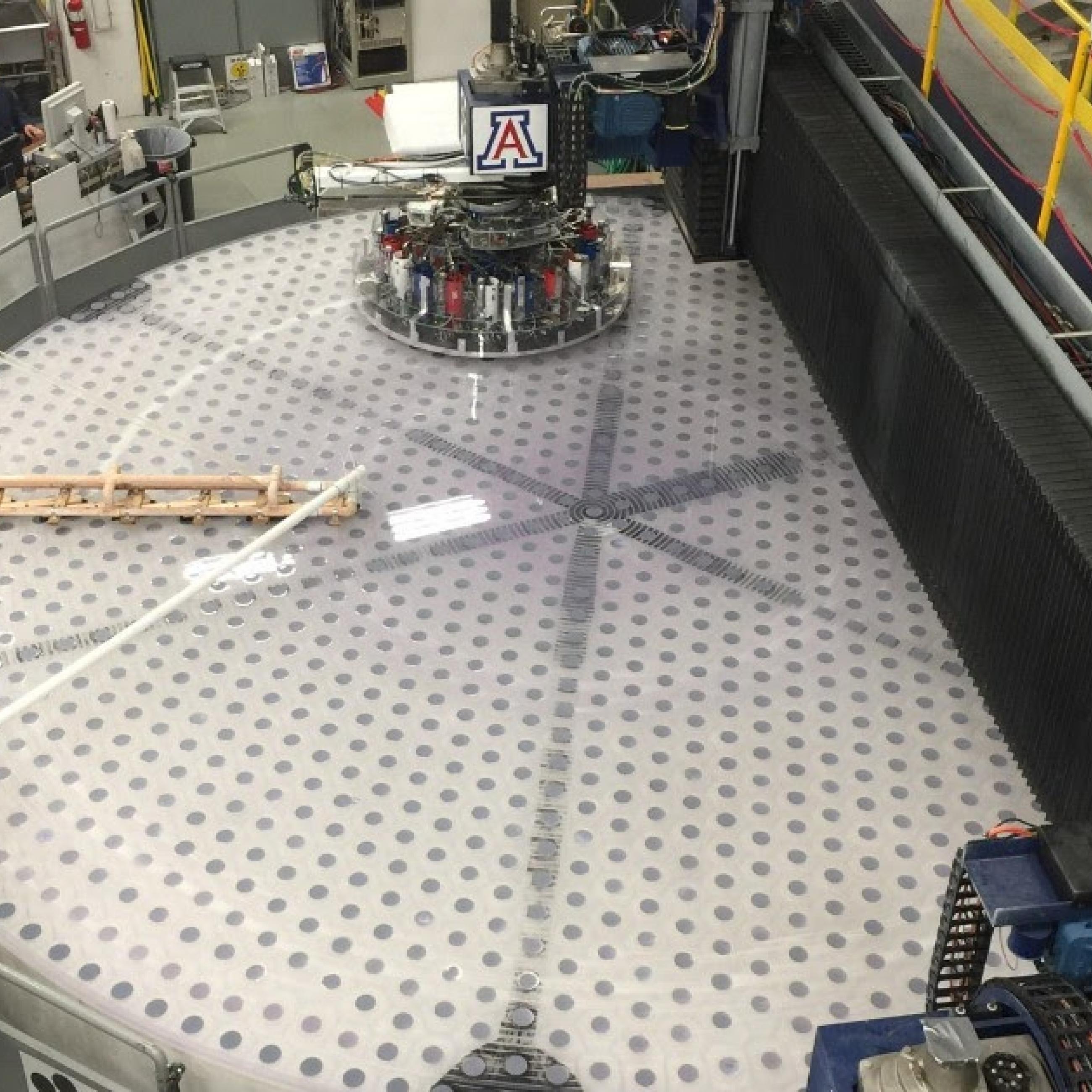
THE PRIMARY MIRROR’S FABRICATION
First, almost 20 tons of glass are melted in a honeycomb-shaped mold, inside a giant rotating oven at 1160ºC for 4 hours. The temperature is cooled rapidly to 900ºC and then it cools slowly for three months to avoid thermal strains. After that, rough grinding of the front and back surfaces is performed.
The front surface is polished with computer controlled tools to achieve optical tolerances that are constantly measured to assure that it is precisely figured.
At the end of polishing, it’s placed on a complex support system and the surface is coated with a thin layer of aluminum to attain maximum reflectivity. The mirror is transported to a local storage facility, where it will remain until the GMT is assembled.